Every year, thousands of preventable workplace incidents cause the injury, illness, and even death of employees. In the 2019 fiscal year, OSHA issued about 27,000 citations in these top 10 categories:
- Fall Protection- General Requirements
- Hazard Communication
- Scaffolding
- Lockout/Tagout
- Respiratory Protection
- Ladders
- Powered Industrial Trucks
- Fall Protection- Training Requirements
- Machine Guarding
- PPE- Eye and Face Protection
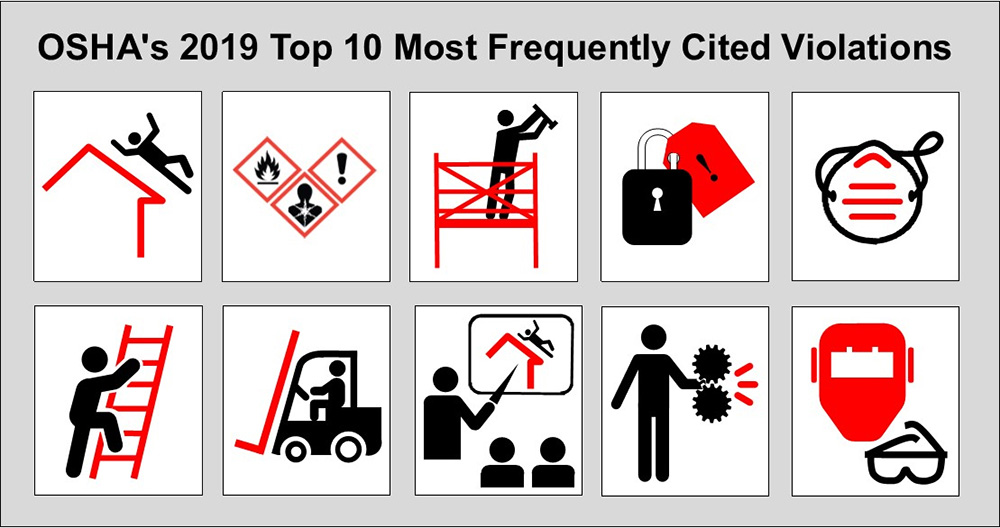
Fall Protection – General Requirements and Training Requirements
Falls are the most common way employees get hurt or killed at work. Employers must prevent employees from falling from platforms and into holes, as well as train workers in fall prevention.
Fall violations are often caused by unaddressed wet and uneven surfaces, poor lighting, defective or misused ladders, crowded workspaces, and dangerous weather conditions.
To protect workers from falls, employers must keep floors clean and dry, cover floor holes, provide guardrails and toe-boards around raised platforms and walkways, provide PPE, train workers about fall hazards, and when required, provide nets, harnesses, and railings.
Hazard Communication
Employees have the right to know what chemicals they are working with, what their hazards are, and how to protect themselves from them. OSHA’s Hazard Communication Standard is designed to provide employees with this important information. Violations often happen because of the complexity and paperwork required.
Common violations include failure to label chemical containers, incomplete chemical inventory lists, and failure to obtain SDS. Not completing or maintaining a hazard communication plan is also a common citation. Violations are also caused by incomplete or out of date employee training.
By ensuring all employees and contractors have access to the Hazard Communication Program and SDS, employees are properly trained, and all chemical containers are adequately labeled, these common citations can be avoided.
Scaffolding
Scaffolding related accidents are a significant cause of death at construction workplaces. OHSA’s scaffolding standard covers supported scaffolds, suspended scaffolds, and aerial lifts, as well as falling objects, ladder, and other associated risks.
According to the Bureau of Labor Statistics, 70% of all scaffolding incidents are due to planks giving out, slippery surfaces, tripping, and falling objects. These situations arise when equipment is faulty, or incorrectly used. Lack of proper employee training also leads to more incidents.
To prevent these kinds of accidents, employees should be trained in proper scaffolding use, scaffolds should be inspected regularly, and fall protection measures like the ones mentioned earlier should be in place.
Lockout/Tagout
The OSHA standard for Lockout/Tagout covers the procedures used to disable machinery or equipment while employees perform maintenance and servicing activities. Electricity, heat, chemicals, and mechanics are all ways machinery can harm workers. Even machines not in use can injure or kill employees if they are not securely disabled.
Violations often happen because lockout/tagout steps are not taken in the correct order. At a minimum, employees must be notified of the procedure, equipment is shut down, the energy source is isolated, the lockout device is engaged, energy in the machine is released or restrained, and the lockout is verified (tagout), in this order. Other common causes of violations are poor documentation of lockout/tagout procedure for every single machine and insufficient employee training for all employees that come near dangerous machines.
To avoid Lockout/Tagout citations, employers need detailed procedures for every machine in use. They also need to ensure the correct lockout/tagout devices are used and that machines and procedures are regularly audited. Employee training is essential, as well.
Respiratory Protection
This standard covers air that is unsafe to breathe. Smoke, fumes, dust, vapors, and aerosols are a few things that can make air unsafe. Exposure to these things can cause short- and long-term health effects. Employers should identify and minimize airborne hazards. If this is not adequate, respiratory devices must be provided to employees.
Common violations include not having respiratory protection programs and inadequate employee training. Other common violations are inadequate medical evaluations and failure to do mandatory fit testing.
To stay in compliance, organizations should find out is respiratory protection standards apply to their workplace and develop respiratory procedures. They should also train employees and provide respirators when necessary. Testing equipment, respirators, and ensuring employee access to medical treatment is also very important.
Ladders
OHSA has standards about using, working near, and designing ladders to ensure worker safety. Stepladders, portable ladders, and fixed ladders are all covered by these standards. Rules about the weight a ladder can bear, its angle and position, rung spacing, and ladder maintenance are also covered.
Most ladder related injuries and deaths are due to falling. Many OHSA violations are due to misuse and mismeasurement. Using the top of a stepladder as a step, using defective ladders, and using ladders for unintended purposes are things that should be avoided.
To prevent citations ladders should be inspected for defects, kept clean and dry, used properly, and employees should be trained on safe ladder use.
Powered Industrial Trucks
The powered industrial truck standard covers rules for equipment like forklifts, such as forklift operator training, safe driving speeds, forklift pedestrian safety, and forklift capacity. Forklift accidents are most often forklifts tipping over and pedestrian accidents.
To avoid citations, forklift operators must be fully trained, certified, and 18 years of age or older. Forklifts should be inspected regularly, and tipping precautions should be taken by watching for weight maximums and load balancing. Operators should observe speed limits, watch for pedestrians, use their horns, and wear safety belt.
Machine Guarding
Machine guarding is the practice of having mechanisms in place that protect workers from dangerous equipment. Certain equipment is capable of severely injuring or killing employees. Amputations, abrasions, lacerations, and crushing injuries are examples of what can happen in an accident.
The leading cause of violation of this standard is poor employee training. Incidents are also cause by a lack of safeguards and poorly designed safeguards. Human error and carelessness also cause accidents.
To avoid these incidents, employees should be trained properly, dangers should be identified, and safeguards should be well designed and inspected for damage.
Personal Protective Equipment – Eye and Face Protection
OSHA requires employers to supply workers with PPE when not having it could lead to injury or illness. PPE must be regularly inspected and maintained, fit comfortably and properly, and be fit for the job or working condition. Dysfunctional PPE must be replaced.
Eye and Face protection standards are often violated because eyes and faces are under protected. When employees are not properly trained in how to use their PPE, they may take it off too soon, wear it improperly, or not wear it at all. Inaccessibility of correct and well-fitting PPE is another reason for PPE violations.
To avoid PPE citations, PPE should be in good condition and properly stored. Employees should be trained how to use PPE, as well as when to use it and how to take care of it. Hazards and PPE requirements should be communicated to employees both through training and signs.
Want to learn more about frequently cited OSHA Standards?
Visit OSHA’s Top Ten frequently cited standards.