OSHA’s Hazard Communication Standard (29 CFR 1910.1200) addresses the classification and communication of the hazards and potential hazards of chemicals. It requires employers to provide information to their employees about the hazardous chemicals they are exposed to at their workplace as well as the protective measures against these hazards.
Employers must meet these requirements by methods including, but not limited to:
- Developing and maintaining a workplace hazard communication program
- Maintaining lists of the hazardous chemicals present
- Labeling containers of chemicals in the workplace and chemicals being shipped to other workplace
- Providing employees with up-to-date and readily available Safety Data Sheets (SDS) for all chemicals found at the workplace
- Training employees in hazard communication and protective measures
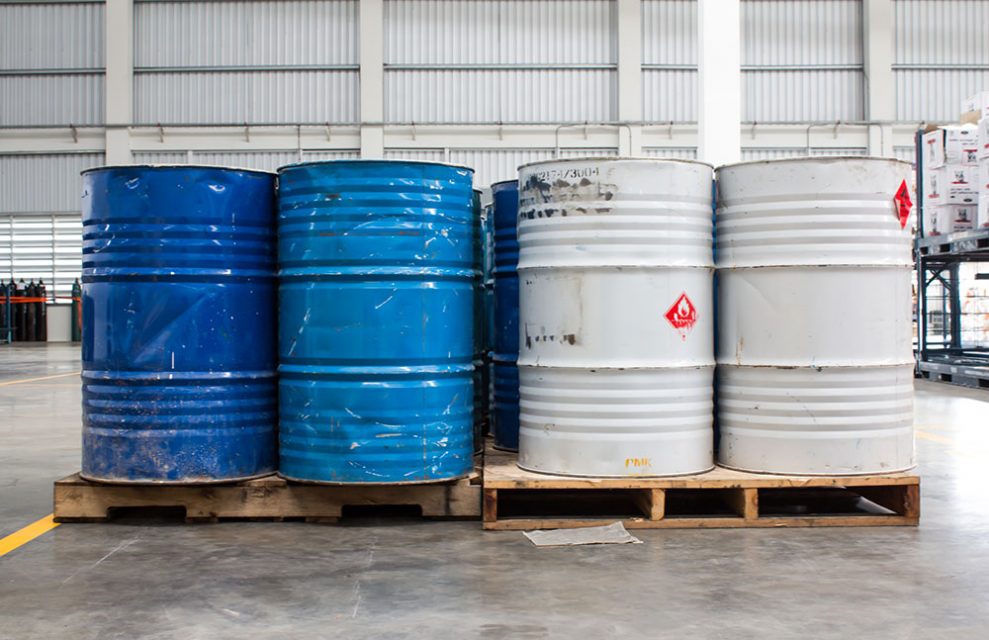
Written Hazard Communication Program
According to OSHA Standard 29 CFR 1910.1200, employers must develop, implement, and maintain a written hazard communication program at each workplace. This plan must include how the criteria for labels and other warnings, safety data sheets, employee information and training will be met. The plan must also include a list of the hazardous chemicals known to be present (workplace wide or specific area), and the methods the employer will use to inform employees of the hazards associated with non-routine task and chemicals contained in unlabeled pipes.
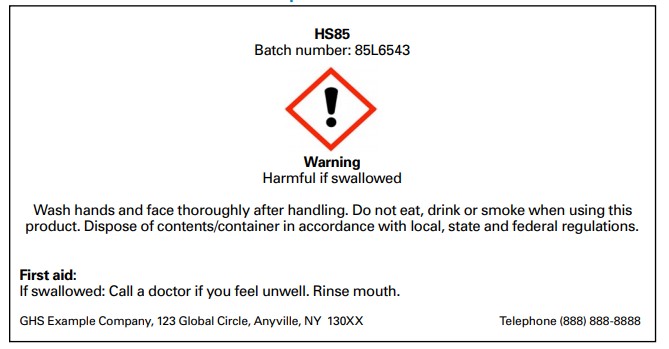
Labels and Other Forms of Warning
Employers must ensure that containers of hazardous chemicals are labeled, tagged, or marked with relevant information including the product identifier, hazard statement, pictograms, precautionary statement and the name, address, and phone number of the chemical manufacturer, importer, or other responsible party. Labels must be legible and in English. Other languages are optional. Employers may not remove or deface labels on incoming containers unless the container is immediately labeled with the required information.
Safety Data Sheets
Employers must have a safety data sheet (SDS) for every hazardous chemical in use. SDSs must be readily accessible to employees during each work shift when they are in their work areas. The safety data sheets may be kept in any form if the required information is provided, and employees can access SDS within their work areas.
Safety data sheets should also be readily available to designated representatives in accordance with §1910.1020. This OSHA regulation requires employers to keep records of hazardous chemicals that employees are exposed to for 30 years. A chemical inventory that reveals when and where a chemical is used and the identity of the chemical can be used instead to satisfy 29 CFR 1910.1020 but it is often easier to keep an archive of safety data sheets to meet this standard.
Employee Information and Training
Employers must provide employees with effective information and training on hazard chemicals in their work area at the time of their assignment and whenever a new chemical hazard is introduced. Information specific to each chemical must always be available through labels and safety data sheets. Employees must be informed of all operations where hazardous chemicals are present in their work area and the location and availability of the hazard communication program, as well as the list of hazardous chemicals and the safety data sheets.
Employee training must include:
- Methods to detect the presence or release of hazardous chemicals
- Explanation of the physical, health, simple asphyxiation, combustible dust, pyrophoric gas hazards as well as other hazards in the workplace
- Protective measures such as appropriate workplace practice, emergency procedures, and PPE
- Explanation of labels on shipping containers and workplace labeling, safety data sheets, and how employees can obtain and use hazard information.
Would you like additional Hazardous Chemical Information?
Visit OSHA’s Hazard Communication program.